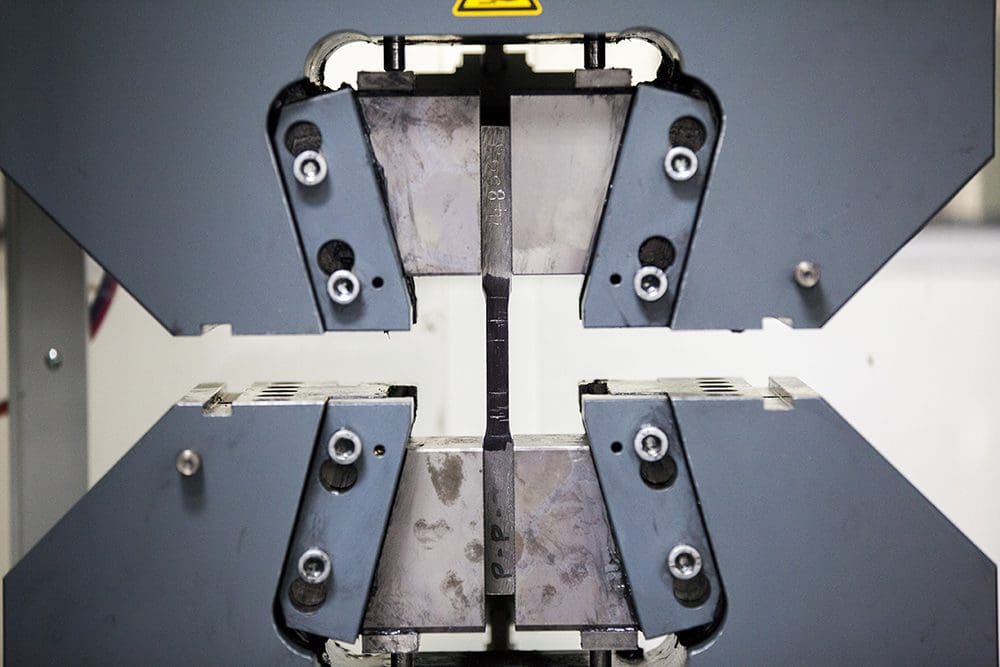
Destructive Testing (DT)
Unveiling the inner strengths of your materials
Destructive Testing (DT) uses destructive techniques to assesses a materials properties, performance, and safety of your materials, products, and components by subjecting them to test conditions that provide an insight into how materials will performs when in use. It gives you insights into the durability and reliability of your items. It also ensures they meet industry standards and regulatory requirements, helping you avoid product failures and reduced lifespans.
Destructive testing services from BES Group
At BES Group, we offer a variety of destructive testing methods to ensure the quality, safety, and reliability of your materials and products. We provide UKAS and NADCAP-accredited tests to help a variety of clients across industries such as aerospace, manufacturing, and healthcare use safe, reliable assets.
Our in-house capabilities provide quick and accurate testing results, which helps minimise downtime and ensure you get the critical data you need. Below is a summary of our destructive testing services:
Destructive testing services from BES Group
At BES Group, we offer a variety of destructive testing methods to ensure the quality, safety, and reliability of your materials and products. We provide UKAS and NADCAP-accredited tests to help a variety of clients across industries such as aerospace, manufacturing, and healthcare use safe, reliable assets.
Our in-house capabilities provide quick and accurate testing results, which helps minimise downtime and ensure you get the critical data you need.
Below is a summary of our destructive testing services:
Tensile Testing
Impact Testing
Hardness Testing
Chemical Analysis
Metallography
Corrosion Testing
Weld Testing
Finish Testing
Schedule a call to learn more about our destructive testing services
Get in touch with our destructive testing experts today Get in touch with our destructive testing experts today Get in touch with our destructive testing experts today
All your destructive testing needs in one place
At BES Group, we handle all your metals testing in one place to make things easier and more efficient.
We know sending samples to multiple labs for different testing methods can be frustrating. Not only is it expensive to machine and send multiple samples, but inconsistent results can occur if the labs use samples from different heat-treated batches.
Our unique benefits include:
- Comprehensive testing suite: We offer a full suite of tests to thoroughly examine your sample’s properties, structure, and behaviour.
- In-house sample preparation: Our in-house workshop prepares the samples tested in our UKAS-accredited laboratory for consistent and reliable results.
- Efficient sample tracking: Each sample is assigned a unique barcode so we can monitor its progress from arrival to testing completion.
- Rapid turnaround: To minimise downtime and delays, we aim to complete our full suite of destructive tests within three to five
Key benefits of our destructive testing
Material verification
Confirms that materials meet required specifications and industry standards, ensuring reliability and performance.
Weld quality determination
Assesses the quality and integrity of welded joints, which is critical for structural applications
Defining asset limitations
Helps identify the limits of materials and components, enabling the creation of plans to reduce failures, accidents, and costs.
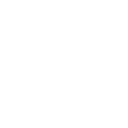
Impact resistance assessment
Determining how well materials can withstand impacts and shocks is essential for safety-critical applications.

Failure analysis
Provides detailed insights into how and why materials fail, leading to improved product design and manufacturing processes.

Regulatory compliance
Ensures that products meet industry-specific regulations and standards, which is crucial for market approval and safety certifications.
Destructive Testing FAQs
Why is Destructive Testing necessary?
+
Destructive Testing is vital for several reasons:
- Material verification: Confirms that materials meet required specifications and standards.
- Safety assurance: Ensures that components can withstand expected loads and stresses, reducing the risk of failure in critical applications.
- Quality control: Helps identify manufacturing defects and inconsistencies, leading to improved product quality.
- Performance evaluation: Provides detailed information about material properties, such as tensile strength, impact resistance, and fatigue life.
- Regulatory compliance: Ensures products meet industry-specific regulations and standards, which is essential for market approval and safety certifications.
What is the purpose of Destructive Testing?
+
Destructive testing aims to understand how a material will react to extreme stress or loads. Knowing how much stress a material can withstand before complete failure is critical when planning to use that material for a key engineering design, manufacturing process, or product design. Destructive testing is usually carried out according to International Standards or bespoke test methods that align with customer requirements.
Our Destructive Testing services include:
- Full machining and preparation of samples
- Tensile, impact, and hardness testing
- Chemical analysis
- Metallurgical examinations
- Corrosion analysis
- Optional services include salt spray testing, weld assessments, and coating finish testing.
Contact us today about Destructive Testing
What are some standard methods of Destructive Testing?
+
Common Destructive Testing methods include Hardness Testing, Impact Testing, Tensile Testing, Fatigue Testing, Bend Testing, and Torsional Testing.
Find the right Destructive Testing method for your premises
What is the difference between Destructive and Non-Destructive Testing?
+
Destructive Testing of materials (DT) involves examining its properties and performance by subjecting it to stress, strain, or other conditions until it fails. This process provides detailed insights into the material’s strength, durability, and failure modes but results in the destruction of the sample.
On the other hand, Non-Destructive Testing (NDT) evaluates the properties of a material or component without causing any damage, allowing the item to remain in service. NDT methods include ultrasonic, radiographic, and magnetic particle testing, which help detect internal or surface defects without altering the material.
Why do I need Destructive Testing?
+
Destructive Testing is crucial in designing, manufacturing, and ensuring product quality across various industries. It provides insight into how much stress a sample can withstand within its intended environment, making this information crucial when deciding whether a particular material or product is suitable.
Learn more about Destructive Testing
Can Destructive and Non-Destructive Testing be used alongside each other?
+
Destructive and Non-Destructive Testing can be used together to assess materials and components comprehensively. NDT methods can initially screen materials for defects and irregularities, allowing for non-invasive evaluation. Following NDT, DT can be performed on selected samples to get deeper insights into the material’s performance and properties. Both methods allow for a thorough evaluation and ensure the highest safety and quality standards.
What industries or products often require Destructive Testing?
+
Destructive Testing is crucial for industries and products where material integrity and performance are critical.
Common industries include:
- Aerospace: To ensure the safety and reliability of aircraft components.
- Automotive: To validate the strength and durability of vehicle parts.
- Construction: To test the quality and safety of building materials like concrete and steel.
- Manufacturing: To verify the properties and performance of manufactured goods.
- Healthcare: To ensure the safety and functionality of medical devices and implants.
- Oil and gas: To assess the reliability of pipelines and drilling equipment.
How would I know what type of Destructive Testing method I need?
+
The material’s standard or specification usually advises the type of Destructive Test. Our customers then instruct us on what type of Destructive Test they require. An unknown material must be identified before a destructive test can occur.
Our technologists will conduct chemical analysis tests to identify chemical properties within the material and determine what the material is. We will then provide this information to our customer, and if further testing is required, we will carry out Destructive Tests to identify the grade of the material. We work with our customers to develop a testing plan to identify the material composition and grade for destructive testing.
Why choose us
Hear what our customers have to say
We care about the journey we take our customers on, but it’s not our word you should be taking, see what our customers think of the service we provided!
Related services
Non-Destructive Testing
Asset Reliability
Structural Investigations, Testing and NDT
Periodic, Intermediate & Vapour Tightness Testing
Our sectors
View all our sectors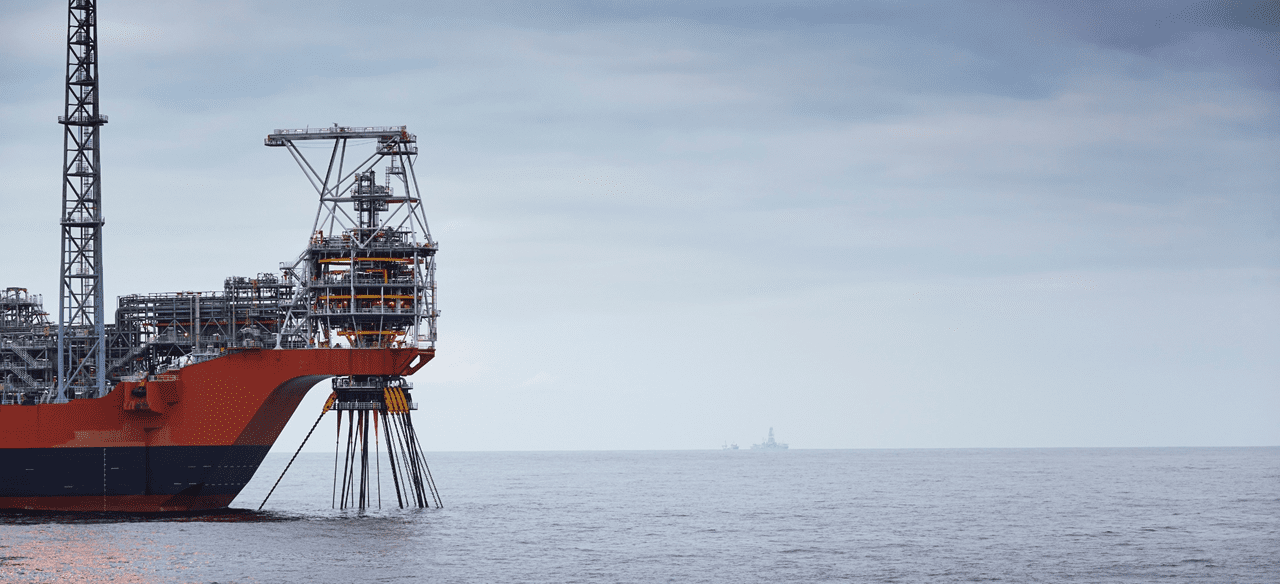